Lean Coordinator Sets the Stage for Savings
Lean manufacturing—the elimination of waste
As a kid, I wanted to be an inventor. I wanted to help people. No one had told me what an engineer was or what they did, but I knew what an inventor was. It took a couple of years in college to figure out that inventing and helping others really meant being an engineer. As the Lean Coordinator of Manufacturing and Engineering at Design Ready Controls, I’ve found the opportunity to create, re imagine and reinvent processes, and to eliminate waste and improve efficiencies across all metrics.
Lean manufacturing—the elimination of waste—can mean different things to different people. And it can be difficult to foresee what someone comes in the door believing about lean. I think it’s important to define lean manufacturing in a positive way– as a way for the entire company to be better. Change can be difficult for anyone, but putting the focus on reducing manufacturing waste and improving efficiencies can help ease the strain. By empowering others to take part in the process—and ownership of their work area—they can provide some of the best insights.
Operators are one of a company’s greatest resources, and they are the experts in the work they do. Given the right support, operators are lean’s greatest advocates.
Respect
One of the tenants of lean is respect for the people, and a lean coordinator respects people by reducing strain, eliminating disruption, and providing the tools they need to do their jobs. The coordinator can balance system improvements and their effects on others by asking managers how their operators perform jobs and then asking operators what pain points they experience. This can prevent a critical function from being overlooked or a process being implemented that works in theory but not in practice. A lean coordinator can balance those process improvements and reduce any resulting disruption, ensuring everyone’s interest is represented within the bigger picture.
Bigger Picture
It’s essential to see that big picture, to have a holistic knowledge of the processes you’re working with. 5S is an important part of waste reduction and cost savings, but a lean coordinator provides a holistic understanding of the complex systems within manufacturing to offer high-level solutions. A comprehensive understanding of the entire system of inputs and outputs along the line prevents unintended disruptions upstream or downstream. Substantial improvements require strong leadership and a broad understanding of lean principles backed by data.
Exciting Challenges
Integrating lean principles in a time of automation, big data and the Industrial Internet of Things (IIoT) is challenging but exciting. There’s so much data to consider. Design Ready Controls uses an advanced ERP and our own Automated Manufacturing Expert (AME®)—a paperless manufacturing system—to track details of each control panel and wire harness build. As the lean coordinator, I help ensure that such a large amount of information is properly synthesized and the most effective lean principle applied—such as Pull Systems and Kanban, standardized work, takt time, Just-In-Time, and Total Productive Maintenance, or others.
Top Lean Manufacturing Tools
Lean tools and techniques are well established and have provided measurable results over the years. We’ve found success implementing top lean manufacturing tools at Design Ready Controls, such as:
- Kaizen
- 5S
- Key Performance Indicators
- Root Cause Analysis/5 Whys
- Just-In-Time
- Gemba
- Visual factory
- Value Stream Mapping
New Lean Chapter
Having a lean manufacturing coordinator has opened a new chapter for Design Ready Controls and for me. We’ve cut costs, reduced waste, and improved efficiencies across the board. It’s reduced our impact on the environment and helped us re-purpose unused supplies and equipment, allowing us to donate over 16 pallets worth of materials to local tech colleges.
I’ve always been motivated to help others—whether it’s improving ergonomics for my coworkers, re-purposing equipment for schools, or providing people with the best tools to do their jobs. Working as a lean coordinator has opened the door for me to spend my days inventing, innovating, and helping the people around me—exactly what I’ve wanted to do since I was a kid.
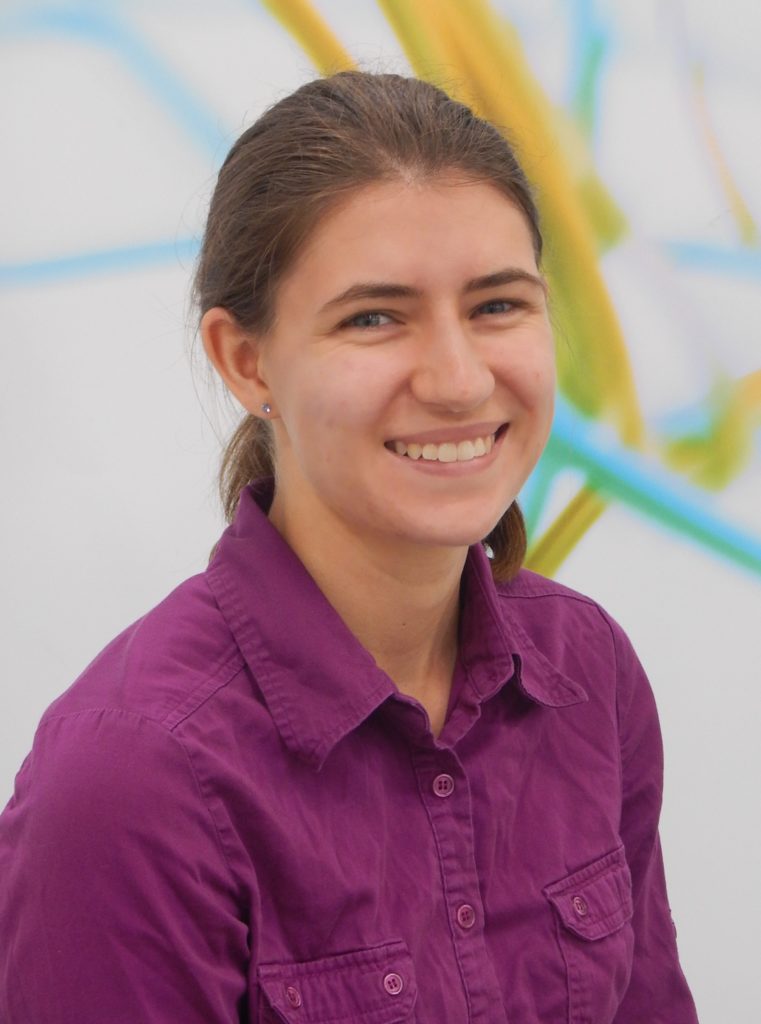