A New Twist on Torque Quality
A Culture of Continuous Improvement
At Design Ready Controls, we have always challenged the standards of control panel manufacturing. In more than a decade of growth and innovation, we have never stopped searching for ways to improve process efficiency and product quality. We examine and push to improve all practices, regardless of their current level of success. One of those practices is the proper tightening of connections and hardware, what we refer to here as torqueing.
Components of a control panel have a variety of connection specs that must be met—such as torque values—to assure the overall quality and safety of the end unit. These components can shift, loosen, or become disconnected during transport. Those at highest risk are connections not properly torqued. Tightening a connection either under or over the set torque value can cause a variety of issues such as disconnection, breakage, stripped connections, or component damage. Visual inspection alone may not catch either kind of error. Left undetected, torque problems increase the risks of equipment failure over time, including the potential for an electrical fire or arc flash.
To ensure we’re providing the highest quality control products, we recently modified our torque process in a few ways.
Isolating the Torque Process
We created a new torqueing work center, separating this step from the rest of the production process. Adding this station to the line reduces the number of tasks crew members need to perform upstream. They can focus on other responsibilities with fewer interruptions. This also reduces the number of tools each station has to calibrate and maintain. Only select employees—properly trained and equipped—perform torqueing: those at the torque work station, and some in testing and staging.
Torque Training and Certification
We have always trained production employees in applying torque. That’s not new. What’s new is a two-part training program developed specifically to address proper torqueing technique. Design Ready Controls employees conceived, wrote, and produced videos on proper torque tool use, setting torque on digital tools, calibration, torque marking, application, quality, and best practices.
After completing the video portion, employees receive a guided presentation and hands-on training. A trainer observes the employee applying torque and monitors the process until the employee reaches a demonstrated level of proficiency. A Certification of Training is then signed to document that employee’s proficiency.
To prevent duplication and reduce the potential for error, we also “untrained” other production employees—communicating that they no longer needed to apply torque. The importance of this is to ensure fasteners are not over torqued. The torque operator should be able to rotate the fastener up to the final torque. If fasteners are over-tightened or over torqued upstream, the final torque operator would not have rotation on the fastener.
Torque Database and Advanced Automation
Because we make control panels at a high volume with high variability to meet the specifications of original equipment manufacturers, every panel we make is different. This means no two panels will have the same torque requirements, and our employees always needs to know what they are.
Torque information has always been available, but from a variety of sources. Some are on a label on the side of a part, on the component packaging, or on a separate document entirely. We gathered all torque data into a report, providing a single point of reference for most common values. But with such high variation, there were still gaps in this torque table.
To improve on it, we collected all torque information into a torque database. When a job is run, our Automated Manufacturing Expert (AME®) system pulls information from that database and creates a spreadsheet listing components, term points, torque values, and torque tools.
This presents variable information to production as if it weren’t a variable at all. Torque values are displayed only for that particular part and build. Employees don’t need to scan through unnecessary parts and values to get the information they need. Only relevant information is presented, increasing efficiencies and reducing the potential for error.
Near Future Innovation with Smart Torque Tools
Design Ready Controls has a decade of solid growth behind it and a record of innovation. As we grow and leverage new technologies, our push is toward continued automation. Smart, wireless torque tools are the next step. These tools will automatically load the specified torque values and adjust each connection to the required torque, in order. The tool sends data back to our system to confirm the torque applied. The system would generate a flag if a connection is missed or torqued a second time.
Smart tools—utilizing the Industrial Internet of Things—can also apply modified torque, such as a partial torque. Not all strands within a wire immediately settle into their final resting spot, especially before the end of the assembly process. A partial torque allows an assembler to apply some torque then return to finish torquing when the wires land in their fully seated position. Smart tools would make the process simpler and smoother, ensuring consistent results and reducing the potential for human error.
More Connections to Make
Everything comes back to continuous improvement. Automation and Industrial Internet of Things (IIoT) adoption is an important part of our process management efforts, opening the door for improved efficiencies and workflow. Smart tools can follow instructions, but they can’t make decisions or interpret information the way humans can. By joining human innovation and automation technology, we’re able to meet the challenges of modern manufacturing.
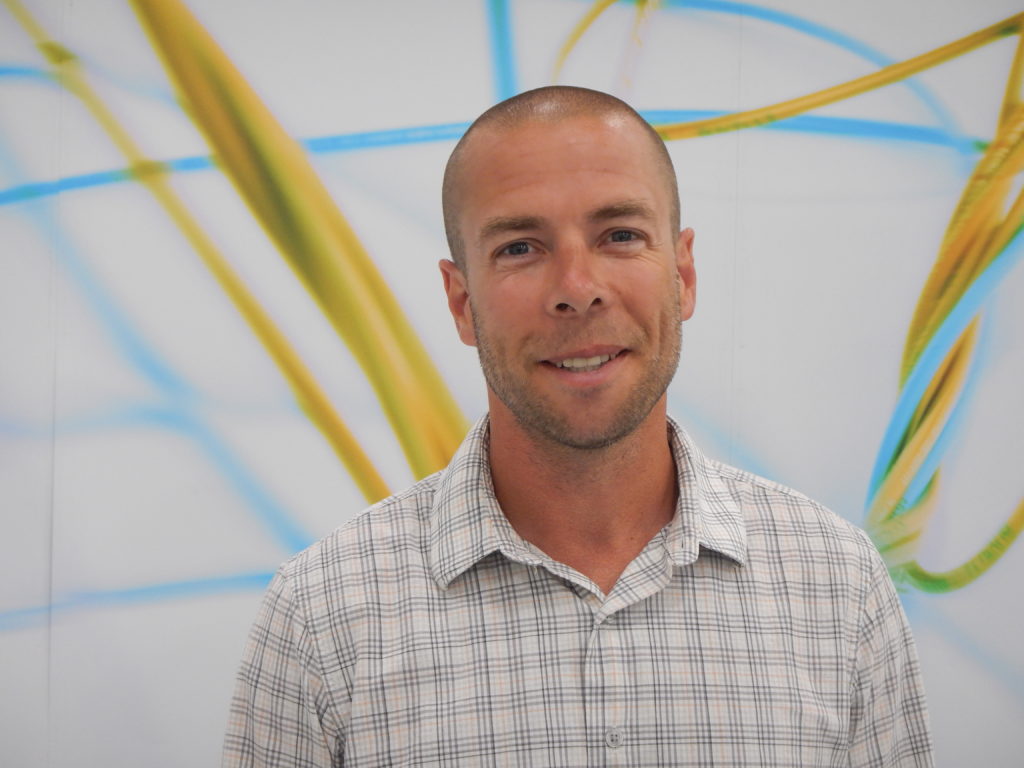